Este artigo é um complemento ao nosso conteúdo sobre os livros que todo profissional de gestão da manutenção deveria ler. Durante a leitura, você vai encontrar os tipos de manutenção mais comuns e as estratégias mais adotadas pelos profissionais da indústria.
O objetivo aqui não é estabelecer uma divisão definitiva dos tipos de manutenção, mesmo porque não há consenso universal nesse sentido. Vários autores propõem diferentes classificações, e uma espécie de taxonomia sobre o tema consolidada e adotada sem alterações ainda não existe. Além de que, com o tempo, novos métodos surgem para atender às necessidades da indústria.
Sendo assim, nós resolvemos adotar livremente critérios próprios para definir essas classes, de acordo com o entendimento dos profissionais da equipe da JW Engenharia.
Mas afinal, o que é Manutenção Industrial?
A manutenção industrial é um conjunto de intervenções que visam garantir o bom funcionamento dos equipamentos. Portanto, o setor de manutenção em uma empresa é fundamental para cuidar do dinheiro que foi investido em máquinas e ferramentas.
Dessa forma, a manutenção de máquinas visa corrigir defeitos, o que, dentro do meio industrial é chamado de manutenção corretiva. Mas o mais importante é a manutenção preditiva, que tem como objetivo impedir que imperfeições apareçam.
Para que serve a manutenção industrial?
A premissa primordial da manutenção industrial é garantir a maior eficiência e disponibilidade de ativos. Para isso, deve-se:
- Otimizar a confiabilidade dos ativos;
- Garantir que os equipamentos estejam sempre em boas condições;
- Reparar imediatamente qualquer máquina.
- Garantir a melhor disponibilidade para a produção;
- Realizar melhorias para aumentar a produtividade;
- Assegurar o funcionamento dos equipamentos de produção;
- Melhorar a segurança operacional;
- Treinar o pessoal de manutenção industrial;
- Assessorar na aquisição, instalação e operação de máquinas;
- Contribuir para a qualidade do produto acabado;
- Garantir a proteção ambiental.
ESTRATÉGIAS DE MANUTENÇÃO
Enquanto os tipos de manutenção industrial se referem à classificação do tipo de ação na realização de um reparo ou ajuste em um equipamento, as estratégias dizem respeito ao planejamento dessa ação, ou seja, em que momento haverá a intervenção da equipe de técnica de manutenção.
Manutenção proativa
Para antecipar problemas e impedir que potenciais falhas parem o equipamento fora do planejado. A manutenção proativa é uma estratégia necessária para empresas que possuem equipamentos em processos críticos, onde qualquer interrupção fora do cronograma compromete a eficiência operacional.
Quando se utiliza a manutenção proativa na estratégia de manutenção de equipamentos industriais, o foco estará em 2 pilares: Confiabilidade da Máquina e Disponibilidade.
As empresas que já adotam essa estratégia possuem uma cultura de manutenção baseada em indicadores, como MBTF (Tempo médio entre falhas) e MTTR (Tempo médio entre reparos). São eles que vão mostrar para os gestores o que o impacto de uma manutenção de troca ou reparo custam para a empresa muito mais do que o valor da peça de reposição.
Nesse sentido, é melhor e menos custoso atuar para que o equipamento não pare de forma inesperada e não impacte na produtividade do processo.
Manutenção reativa
Em contraste com a estratégia anterior, a manutenção reativa são as ações realizadas após o equipamento apresentar o defeito. Ou seja, a empresa opta por intervir somente após o surgimento da falha. Também é conhecida como run to fail, expressão em inglês que significa “operar até a falha”.
A estratégia de manutenção reativa, não é indicada para equipamentos críticos ou de alto impacto nos processos. Visto que a parada de máquina não programada tem consequências significativas para o processo. Deixar para agir somente depois que o problema surge, é um risco muito alto, têm impactos para empresa, como:
- Pode não ter a peça de reposição em estoque,
- Vai exigir uma equipe de manutenção sempre de prontidão,
- Os reparos precisam ser corrigidos de forma rápida,
- Uma falha em um componente relativamente simples, pode afetar outro componente mais importante,
- Atrasos de produção.
Sem dúvida, este tipo de estratégia é o mais caro porque provoca aumento nos custos de manutenção.
Agora que já explicamos quais são as estratégias de manutenção, vamos aos tipos.
TIPOS DE MANUTENÇÃO INDUSTRIAL
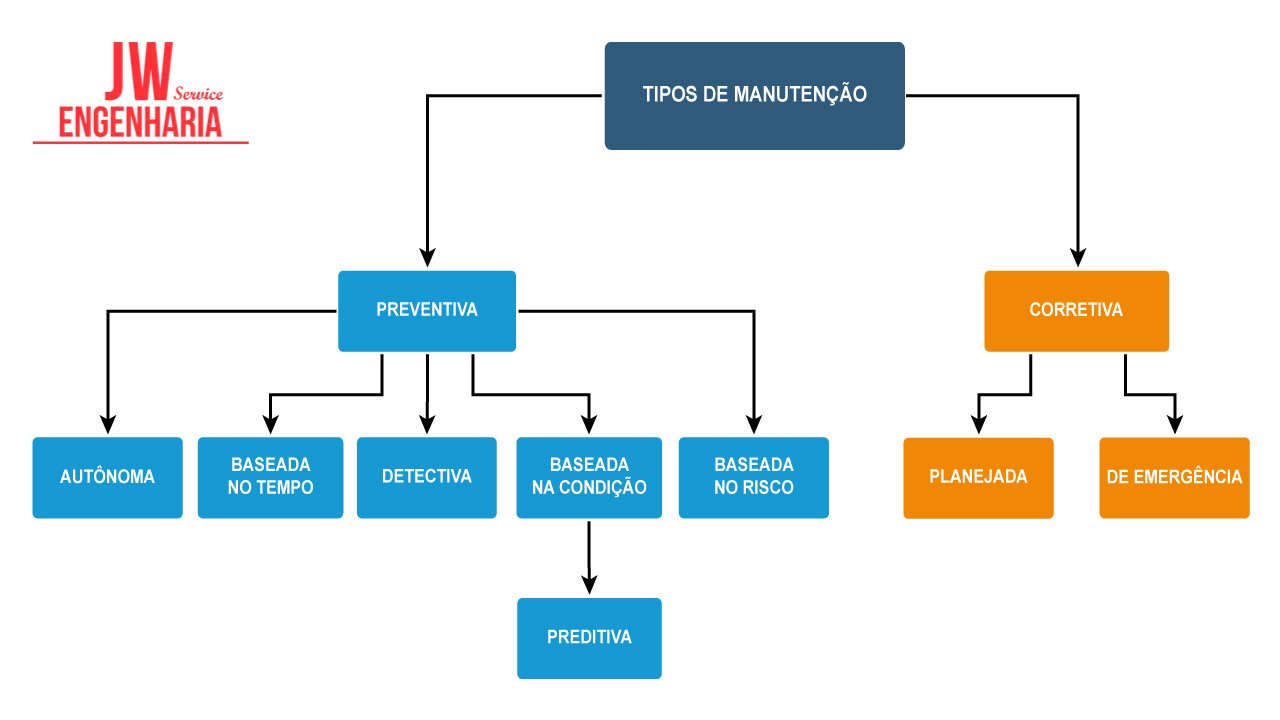
MANUTENÇÃO PREVENTIVA
Geralmente, a manutenção preventiva ocorre através de inspeções regulares, pré-programadas ao longo do ano de acordo com critérios técnicos de previsibilidade do tempo de vida útil dos componentes. O objetivo dessa estratégia é reduzir o risco de falha inesperada e, por conseguinte, a queda de performance dos equipamentos.
Os procedimentos mais comuns envolvem, por exemplo, pequenos reparos, ajustes profiláticos, limpeza de componentes, lubrificação, substituição de peças que atingiram as horas de trabalho projetadas e outros.
A manutenção preventiva faz parte do planejamento de um grande leque de tipos de negócios altamente relevantes para a economia, incluindo produção de comida e de tecidos, manufatura, óleo e gás, mineração, siderurgia, hospitais etc.
Vantagens da manutenção preventiva:
-
- Regularização do ritmo de produção: ao prevenir falhas ou paradas nas máquinas, a manutenção preventiva proporciona uma estabilidade ao processo produtivo. Ademais, por já se saber de antemão qual atividade será realizada pela equipe de manutenção, o estoque de peças pode ser melhor planejado.
- Otimização da escala de trabalho: Sabendo previamente em que momento se realizará a manutenção, é possível recrutar o pessoal de acordo com a vazão produtiva do maquinário, evitando a formação de gargalos ou a improdutividade da mão de obra.
- Economia no orçamento dos itens de estoque: havendo mais tempo para pesquisa e negociação com fornecedores, o custo de compra é potencialmente reduzido.
- Prolongamento da vida útil do maquinário: as inspeções e reparos periódicos conferem uma condição operacional que preserva a durabilidade dos equipamentos.
Desvantagens da manutenção preventiva:
-
- Desperdício de peças: ao substituir uma peça antes que ela apresente algum problema, há uma chance de troca prematura, o que implica em desperdício no inventário de estoque.
- Maior custo de implementação: a necessidade de planejamento prévio para a execução das tarefas requer gasto de tempo; e inspeções e aprimoramentos requerem investimento financeiro contínuo. Conforme demanda e o tamanho da escala produtiva, pode ser necessária a contratação de técnicos com dedicação exclusiva.
Os tipos de manutenção preventiva podem variar de acordo com as necessidades específicas do negócio. Devem incluir uma inspeção cuidadosa dos maiores ativos comerciais da empresa, ou dos equipamentos mais importantes para as operações produtivas. A seguir, veremos os mais comuns.
TIPOS DE MANUTENÇÃO PREVENTIVA
MANUTENÇÃO AUTÔNOMA
Neste caso, o operador do equipamento recebe treinamento para realizar algumas tarefas de manutenção. Ele fica com a responsabilidade de prevenir defeitos e realizar reparos mais simples no equipamento. Essas tarefas incluem lubrificação, limpeza, aperto de parafusos, inspeção de alguns componentes etc.
Geralmente, quando um equipamento é novo, é razoável implementar esse tipo de manutenção através das recomendações do fabricante. Afinal, nesse caso, provavelmente ele tem um melhor entendimento a respeito de seu funcionamento do que o técnico ou operador. Já com o tempo de uso, problemas mais complexos e não previstos pelo manual do fabricante podem surgir, o que demanda uma avaliação especializada.
A vantagem da manutenção autônoma é que ela poupa recursos ao dispensar o acionamento do técnico para a resolução de problemas mais simples. A desvantagem é que as orientações do fabricante seguem uma média estatística de uma base amostral, e não a condição do equipamento específico. Isso pode levar a problemas imprevistos, o que implica em potencial interrupção da produção ou maiores gastos por causa da urgência de reposição.
MANUTENÇÃO BASEADA NO TEMPO DE USO
Esse tipo de manutenção prevê a substituição ou ajuste de um componente com base em um intervalo de tempo fixo ou quantidade de uso predeterminada, independente da sua condição.
O propósito é evitar a falha ou quebra relacionada ao tempo de uso de peças que têm duração de vida útil previsível. Dessa forma, não é possível gerenciar de maneira efetiva problemas não relacionados ao tempo de uso ou itens que não possuem vida útil predeterminada.
Geralmente, o método deve se aplicar somente a uma pequena fração dos equipamentos, pois as falhas relacionadas ao tempo de uso não são maioria. Caso seja mal aplicado, pode haver uma queima de largada no que se chama de “Curva da Banheira”, conforme ilustrada na imagem abaixo.
MANUTENÇÃO DETECTIVA
As tarefas da manutenção detectiva visam detectar falhas tipicamente associadas a funções protetivas, como válvulas de segurança ou sistemas de alerta com receptores/transmissores. Ela busca detectar avarias que ainda não comprometem totalmente o funcionamento do sistema, mas que, se não forem detectadas, poderão culminar em falhas catastróficas.
Esses mecanismos de função protetiva não são ativados até que ocorra algum problema, logo, em condições normais, não é possível verificar se estão funcionando normalmente. Portanto, é preciso identificar falhas antes de uma eventual situação em que haja necessidade de acionamento desses mecanismos e ele não ocorra.
Apesar de não prevenir as falhas, mas sim detectá-las e corrigi-las, a manutenção detectiva é considerada um tipo de manutenção preventiva porque antecipa falhas em situação de real necessidade.
MANUTENÇÃO BASEADA NA CONDIÇÃO
É um tipo de manutenção que se baseia no monitoramento de performance. Atualmente, a condição do equipamento é avaliada pela detecção de parâmetros do funcionamento da máquina e sua comparação com parâmetros médios de performance. Tudo se trata de encontrar indícios de falhas iminentes na condição física dos componentes e intervir para que elas não ocorram.
O monitoramento pode envolver condições como:
- Temperatura;
- Vibração;
- Velocidade;
- Potência;
- Acústica;
- Umidade.
Primeiro, esses indicadores sinalizam a deterioração ou aumento da probabilidade de falha do equipamento. Se forem ignorados, a deterioração continua até causar uma falha funcional. A janela de oportunidade para realizar a manutenção se encontra entre esses dois momentos, como veremos na imagem a seguir:
A efetividade desse método depende da duração do intervalo P–F. A janela de oportunidade deve ser longa o suficiente para cobrir o tempo necessário ao cumprimento de todas as etapas do processo de manutenção. Uma regra comum é que as tarefas de manutenção devem representar de 30 a 50% desse prazo.
Para tipos de falha que apresentam grande variabilidade do intervalo P–F ou cujo intervalo é demasiadamente curto, o monitoramento de condição não é um método eficiente.
A implementação da manutenção baseada na condição exige um processo eficiente de coleta e análise de dados, tomada de decisão e, finalmente, intervenção. Esse método permite, em longo prazo, uma drástica redução nos custos associados à manutenção, minimizando as falhas e otimizando o gerenciamento de recursos disponíveis.
Além disso, há uma diminuição geral do tempo de parada do maquinário. Em vez de mobilizar uma equipe para inspeções periódicas, é possível deixar o equipamento funcionando até haver indícios de deterioração. Sem falar no aumento da segurança para os operadores, uma vez que se evitam mais falhas.
A desvantagem é o alto custo de implementação. Primeiro, pela aquisição de equipamentos de monitoramento e o treinamento adicional dado à equipe de técnicos que vão configurar e calibrar os sensores desses equipamentos — que também precisam de manutenção. O retorno de todo esse investimento pode ser colhido apenas em longo prazo; algumas companhias relatam uma economia de até 30% em custos de manutenção.
MANUTENÇÃO PREDITIVA
A manutenção preditiva é um tipo de manutenção baseada na condição. A diferença é que os dados são trabalhados em algoritmos complexos, que permitem previsões acuradas de falhas futuras e há o envolvimento de Inteligência Artificial.
Na manutenção baseada na condição, há menos matemática envolvida. É possível reduzir o modelo a três indicadores:
- o primeiro representa a condição atual;
- o segundo representa o limite mínimo, a partir do ponto de detecção;
- o terceiro representa o limite máximo, que precede a falha.
A manutenção preditiva pode envolver até mesmo evitar as condições detectadas pelo método baseado na condição que podem culminar em falhas. Por exemplo, no método comum, se um motor operar numa temperatura acima do normal, isso indica que ele necessita de revisão. Já no método preditivo, há um trabalho para que o motor nem sequer chegue a operar em alta temperatura. Isso envolve uma análise mais profunda de dados e sua manipulação em algoritmos, buscando pistas de que algo incomum possa acontecer no sistema.
Como mencionado anteriormente no tópico sobre manutenção baseada em condição, a desvantagem é o custo de implementação, que é ainda mais alto. Softwares modernos são caros e exigem um treinamento ainda mais especializado para a equipe.
Esse é o tipo mais avançado e intensivo de manutenção, e pode representar quedas de até 75% nas falhas de equipamentos e 45% no tempo de parada.
MANUTENÇÃO BASEADA NO RISCO
O padrão da manutenção baseada no risco envolve análise integrada, mensuração e atividades de teste periódico. As informações que se coletam são observadas no contexto das condições ambientais e operacionais dos equipamentos do sistema, e a partir disso se define o programa de manutenção mais apropriado.
Todo equipamento que apresentar dados anormais é reparado ou substituído. Dessa forma, é possível estender o tempo de vida útil do equipamento e manter a confiabilidade, a segurança e a eficiência em altos padrões.
O objetivo principal desse método é avaliar os riscos e as condições de operação, e a partir disso, delinear quais são os recursos mais escassos para manutenção e os componentes de maior risco em caso de falha. Os equipamentos de maior prioridade na avaliação devem ser inspecionados e sofrer manutenção com maior frequência.
MANUTENÇÃO CORRETIVA
A manutenção corretiva se realiza após a identificação de um problema no equipamento e se divide em duas categorias: planejada e não planejada.
A manutenção corretiva não planejada ocorre quando uma máquina ou um componente falha ou quebra de maneira inesperada (ou esperada) e precisa de reparo. Outro caso não planejado é quando o problema identificado ainda não resultou em uma parada total, mas o alto risco exige manutenção imediata do equipamento.
A manutenção corretiva planejada ocorre, por exemplo, quando um item necessita de reparo, mas não se trata de um problema urgente ou de grande risco.
MANUTENÇÃO DE EMERGÊNCIA
A manutenção de emergência é um tipo de manutenção corretiva não planejada, de caráter urgente. Exige uma resposta de última hora a uma parada abrupta do maquinário ou a uma iminência de parada e engloba questões de saúde e segurança.
Deve-se evitar ao máximo chegar a esse ponto. Além de representar riscos, interrompe bruscamente o fluxo produtivo e aumenta os custos de reposição, que é feita sem planejamento. A aparente economia de custos na falta de inspeção pode custar caro em longo prazo, devido a acidentes ou panes mais graves e sistêmicas.
Os setores de indústria química e construção civil são exemplos de setores que realizam manutenção de emergência.
Produtiva Total
A Manutenção Produtiva Total (MPT) é o processo de utilização de máquinas, equipamentos, funcionários e processos de apoio. Para manter e melhorar a integridade e a qualidade dos sistemas de produção. Assim, a MPT envolve os funcionários na manutenção de seus próprios equipamentos.
O principal objetivo da MPT é melhorar a produtividade reduzindo o tempo de inatividade, melhorando a eficiência dos equipamentos, de uma forma geral.
Manutenção de Quebra
O tipo de manutenção de quebra é feita quando há falha total de um equipamento. Portanto, ela não é programada com antecedência, mas as empresas precisam ter recursos de prontidão sempre para o momento em que a falha acontecer.
Manutenção de Parada
A manutenção de parada também é chamada de “shutdown” e se trata de uma ação em que uma planta ou o processo inteiro é retirado de serviço para que haja alguns ajustes. É o famoso “parem as máquinas!” Porém, o intervalo entre as paradas é de meses ou até mais de um ano.
Gostou deste artigo? Confira em nosso blog outros assuntos para a manutenção de equipamentos industriais.